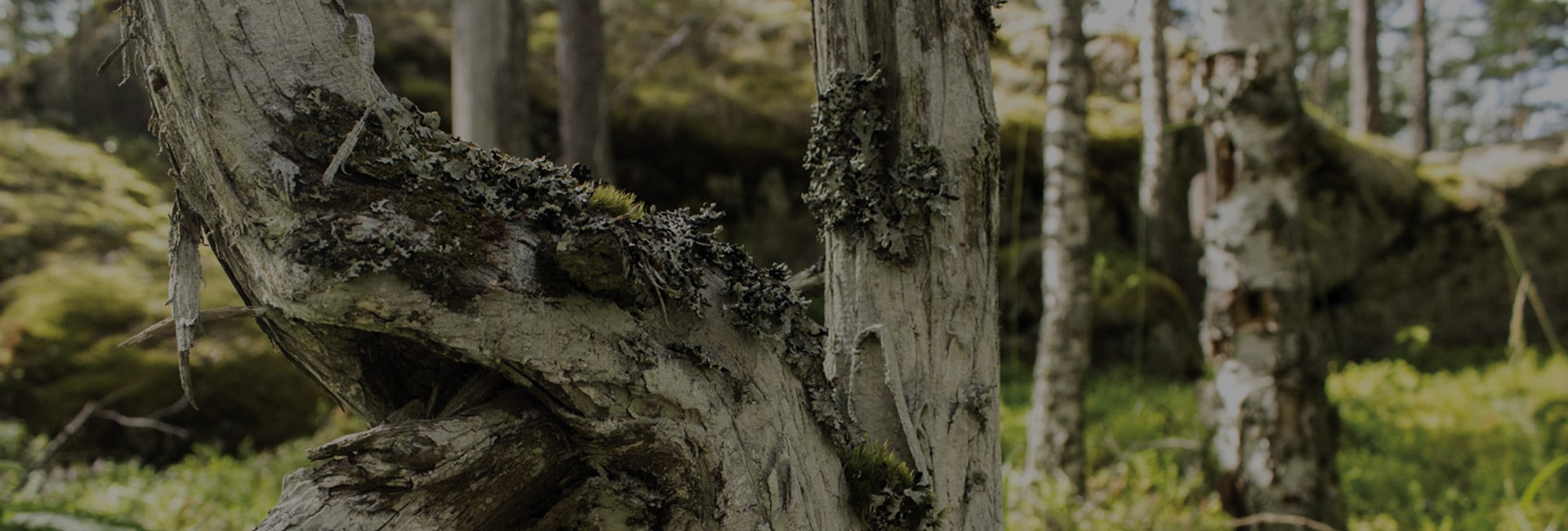
Properties
Materials of possibilities
KARELINE® IS THE FIRST NATURAL FIBRE COMPOSITE THAT IS EASY TO INJECTION MOULD
When designing a completely new product manufactured from a natural fibre composite, reaching the optimal end result requires paying attention to both the possibilities and demands of the material. Kareline® materials give the product designer a new kind of freedom. In mould design, it is advisable to take into account the clearance of nozzles and flow channels, for instance. Listed below is a summary of the properties of the Kareline® materials.
- Unique appearance and tactile feel
- The material does not resemble plastic but rather a natural product in terms of its appearance.
- Almost any colour can be achieved (excluding absolute white and transparent colours). The material can be dyed during injection moulding as usual, providing the end products with a very impressive look. Although coloured, the surface structure of the product retains the depth and natural feel of the Kareline® materials.
- As a general rule, all methods used in the finishing of plastic products (such as hot tool/ultrasonic welding, machine-tooling, surface treatment and different markings, such as laser marking) can be used with the Kareline® natural fibre composites. The same applies to additives, foaming and colouring agents etc. Furthermore, the products provide many options for surface treatment that have never been seen with plastics before. The surface of a composite product can even be waxed or dyed with water-soluble stain.
- Excellent technical properties that give new possibilities for design
- Injection moulded production becomes more efficient thanks to a faster cycle time, and mould design is simplified as a result of small shrinkage and lack of internal stresses in the material. This leads to higher product quality; the pieces can be made straight and even.
- New opportunities for product planning and design: it is possible to manufacture end products with extremely thick walls. On the other hand, the wall thickness can vary very much in a single injection moulded piece and thin walls can also be made.
- Improved technical quality in injection moulded pieces. Kareline® natural fibre composites enable the design and manufacture of products with great dimensional accuracy that are straight and thus of high quality. There are no internal stresses in the products, and the sink marks remain invisible.
- The material has an excellent strength/weight ratio. The material does not cold seal, nor does it have any problems related to recyclability. All Kareline® composites reproduce the surface and structures of the mould with much greater precision than glass reinforced plastics.
- Improved rigidity in the material.
- Wider operating temperature range. Fibre reinforcement widens the operating temperature range of the material in comparison to similar matrix plastic. This is a significant property, especially for biodegradable polymers.
- Eco-friendly and recyclable
The material is environmentally friendly in many aspects. At the end of their life cycle, the products can be disposed of by burning; in contrast to glass reinforced pieces that cannot be discarded easily. Here, one should also note the increasing pressure worldwide to ultimately bring the manufacturer to account for the disposal of products at the end of their service life (producer responsibility). In these cases, using Kareline® composites can provide considerable savings at the end of a product’s life cycle. End products become more competitive with regard to the environment, when a significant share of fossil raw materials can be replaced with renewable ones. If necessary, 100% naturally biodegradable polymers, made from renewable raw materials, can be used as the matrix for the composite.
- Kareline® natural fibre composites are manufactured using EKOenergy.
Properties and benefits in relation to traditional, glass reinforced plastic composites:
- The lack of internal stresses enables the design of new kinds of products, such as ones with thick walls and rib structures.
- The material has excellent dimensional accuracy and stability in manufacturing.
- The appearance and tactile feel of the material can be adjusted.
- The material has an excellent strength/weight ratio.
- Production machinery suffers less wear and tear.
- Kareline® is extremely diversified and well suited for many applications. The material’s appearance and properties can be adapted according to the application.
- The use of wood fibre reduces the environmental load of the plastic material. According to the Kyoto climate treaty, incineration of wood does not increase carbon dioxide emissions.
- The material features excellent recyclability; it can be injection moulded again or disposed of through incineration as energy.
Properties and benefits in relation to natural wood (i.e., to the properties of wood when comparing certain applications and areas):
- The uniform quality of the material is superior compared to wood in terms of both stiffness and other properties.
- Kareline® offers excellent weather resistance in comparison with wood – the material is not sensitive to changes in the environment and conditions, such as moisture, microbes and rot fungi or bacteria. All this can be achieved without using any additives hazardous to the environment.
- The production technology features excellent reproduction accuracy.
- The production technology boasts superior efficiency.
- The material properties can be adjusted to perfection for the end product.
- Kareline® can be welded, so there is no need for glue. However, the material can be glued if necessary.
- The extended service life of the end products decreases their life-cycle cost.
How do Kareline® materials differ from wood plastic composites (WPC)?
The natural fibre used is virgin softwood pulp (cellulose fibre) that is ecologically produced and manufactured – it is not a wood industry by-product such as wood flour, sawdust or wood shavings. The material is thus very different from traditional wood plastic composites as far as properties and applications are concerned. Kareline® composites genuinely reinforce, and other important properties are sought through the use of pure, technical and homogenous natural fibres. Consequently, the mechanical and application properties of the Kareline® composites strongly differ from those of the wood plastic composites mentioned above.
Kareline® composites are at their best when a complex shape is required, combined with excellent strength and recyclability.